In the process of compound feed production, the safe and normal production of the pelletizer is very important, because the preparation of pellets is completely completed by the pelletizer. However, in actual production, due to various reasons, it is easy to form a layer of thick and hard material “cooker” between the ring die and the pressing roller. The pressing roller cannot squeeze the material out of the die hole, making the ring die of the pellet mill stuck. die or slip, resulting in the common phenomenon of granulator blockage.
Through the on-site analysis of multi-equipment and multi-material, in fact, the reasons for the blockage are as follows:
Improper die roll gap of the feed pellet extruder
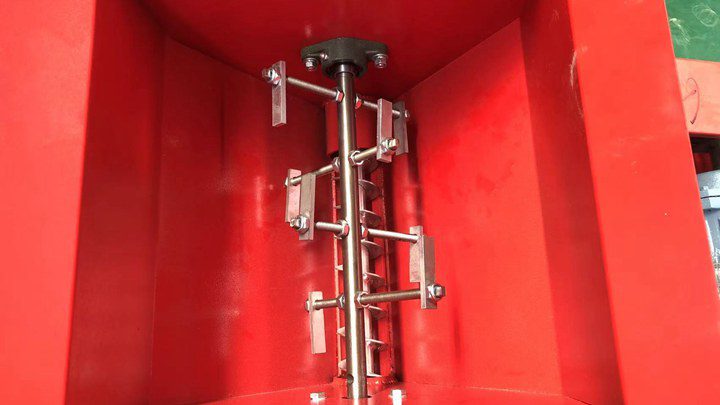
The gap between the die rollers is too large, which causes the material layer between the die rollers to be too thick and unevenly distributed, and the pressure rollers are easily slipped due to uneven force. Once the extrusion force of the die roller on the material is less than the resistance of the inner wall of the die hole to the material, the material cannot be squeezed out and the machine will be blocked. In order to reduce the blockage of the machine, attention should be paid to adjusting the gap between the die rolls during production. When adjusting, the pressure roll, and the ring die to form a state of “like relying on non-depending, like rotating instead of rotating”. According to observation, this gap is generally 3-5mm. In the middle, the experience of the granulator and the adjustment of the feel are very important.
The effect of steam
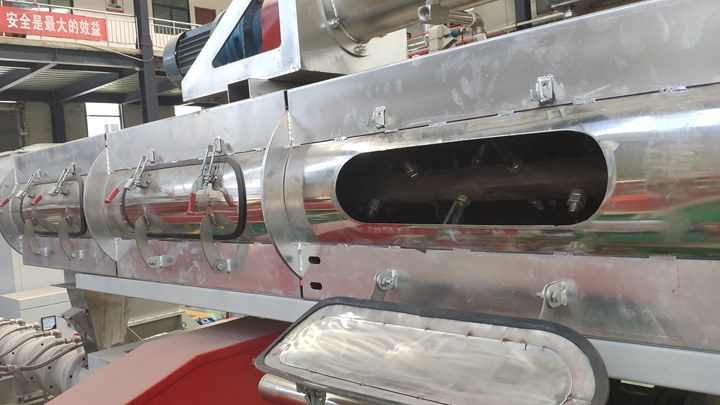
The most ideal production conditions in the production process of pellet feed are: the moisture content of raw materials is suitable, the steam quality is good, and there is sufficient conditioning time. Correct use of dry saturated steam for granulation can effectively improve the output of the granulator and the quality of the pellets. To ensure good quality of pellets and high output, in addition to the normal operation of each transmission part of the granulator, the quality of dry saturated steam entering the conditioner of the granulator should also be guaranteed. Applicable saturated steam has softening and lubricating effect in the granulation process, which can improve productivity, reduce frictional heat energy, and prolong the service life of ring die; it can reduce power consumption, promote the gelatinization of starch and the bonding of fibrous fibers; it can increase the number of granules The molding rate is increased, the powder is reduced, and the surface of the material is smooth and neat, thereby improving the competitiveness of the product.
The quality of steam is poor so that the moisture of the material is too high when it leaves the conditioner, and it is easy to cause blockage of the die hole when entering the granulation cavity, and the pressure roller slips, resulting in a blockage of the machine.
Specific manifestations of the poor steam
1. Insufficient steam pressure and high moisture content make the material easy to absorb too much water. At the same time, when the pressure is low, the temperature of the material when quenched and tempered is also low, the starch cannot be gelatinized well, and the granulation effect is poor;
2. Steam The pressure is unstable, high, and low, and the material conditioning is unstable, resulting in large current fluctuations in the granulator, the uneven thirst of the material, and easy blockage in the normal production process.
Granulators should pay attention to various factors such as steam pressure and conditioner feeding amount at any time, so as to avoid excessive moisture in material conditioning caused by steam pressure and water content. At the same time, in order to reduce the number of blockages caused by steam quality, the boiler room should provide high-quality and stable dry saturated steam. During the production process, the granulator should always pay attention to the moisture content of the conditioned material, which can be determined by a simple method.
Influence of conditioning effect on the material
To make pellet feed meet the competitive demands of the market, it is necessary to ensure its high quality. The conditioning effect of the material before granulation is very important because it directly affects the output of the granulator and the quality of the granules, especially the water stability of the special aquatic product is an important indicator. If the material is not fully conditioned and matured before granulation, the index of its water stability is difficult to guarantee.
The so-called conditioning is the pretreatment of powdery materials before granulation, which is the process of fully stirring and absorbing the powder to be granulated and an appropriate amount of steam in the conditioner. Select the conditioning equipment that meets the technical requirements, so that the material can be fully stirred and mixed with steam in the conditioner to achieve the effect of softening the material and gelatinizing starch, which is conducive to the compaction of the powder and the production of qualified products. The conditioner needs to have a long time of heat preservation, heating, and humidification, and the number of layers can be installed in any combination as required, which can ensure that the material fully meets the requirements of conditioning, improve the surface and internal quality of the granular material, and improve its water resistance in the water.
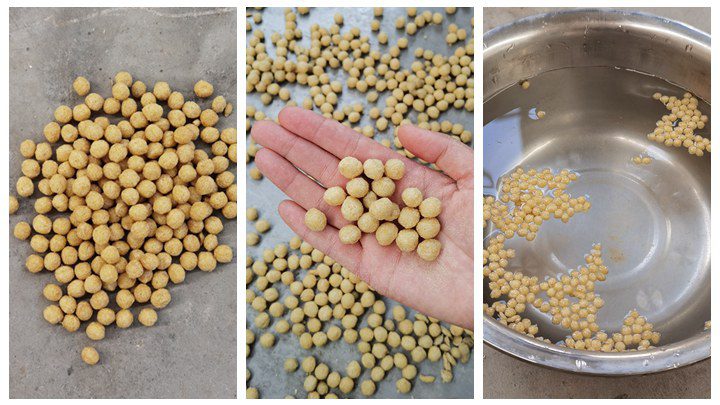
Through on-site debugging, the number of blockages of the pellet machine can be reduced, which can be solved by adjusting the steam. Since the boiler equipment has been finalized, the provided steam has been determined. Pay attention to the treatment method of water vapor in the steam pipeline, try to eliminate the condensed water in the steam pipeline, and the steam pressure at the front end of the conditioner must be very stable.