The feed pelleting machine is the main equipment in the production process of each feed factory, and it can also be said to be the heart of the feed pellet production line. The correct use of the floating fish feed extruder directly affects the economic benefits of the feed pellet. Therefore, how to properly use and maintain the floating fish feed extruder is a major issue for feed factories to improve production efficiency.
Lima floating fish feed pelleting machine is characterized by the use of gear transmission structure, which has the advantages of long service life, high production capacity and low power consumption, and has become the preferred product of various feed factories.
But good equipment also needs correct use and careful maintenance. We have formulated a set of operating procedures and maintenance systems for the floating fish extruder. Due to the meticulous maintenance of the equipment, the hidden danger of equipment failure is reduced, thereby extending the service life of the extruder, reducing the maintenance cost, and increasing the benefits for the enterprise.
Precautions in the operation of the floating fish feed extruder
1. Lubricate the transmission parts of the granulator regularly, lubricate the bearing of the pressure roller every 2 hours, and lubricate the front bearing of the main shaft every 4 hours to ensure the flexible rotation of the transmission parts of the floating fish feed pelleting machine and reduce the workload.
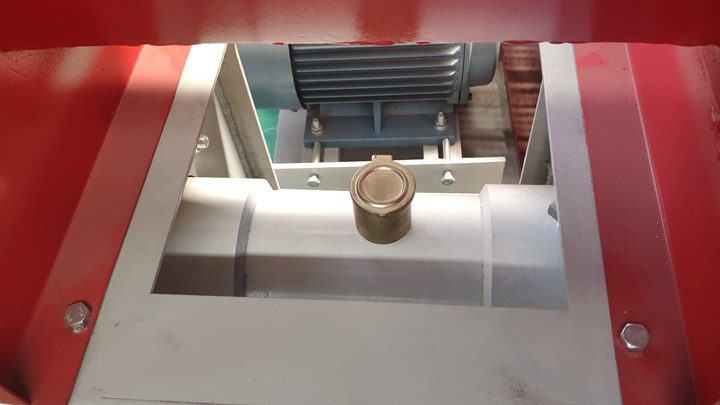
2. Regularly replace the lubricating oil in the gearbox of the granulator. The new machine needs to be replaced once after half a month of operation, and it must be replaced once every 1,000 hours of continuous operation, which can prolong the service life of the gear.
3. Once a week, it is necessary to carefully check whether the connecting parts of each part are loose, whether the stroke safety switch is reliable, and at the same time clean the feeding auger and conditioner to avoid mechanical failure.
4. Check the wear of the drive key and the die lining and the hoop every half month, and replace it in time if the wear is found to avoid the ring die shaking and affecting the output.
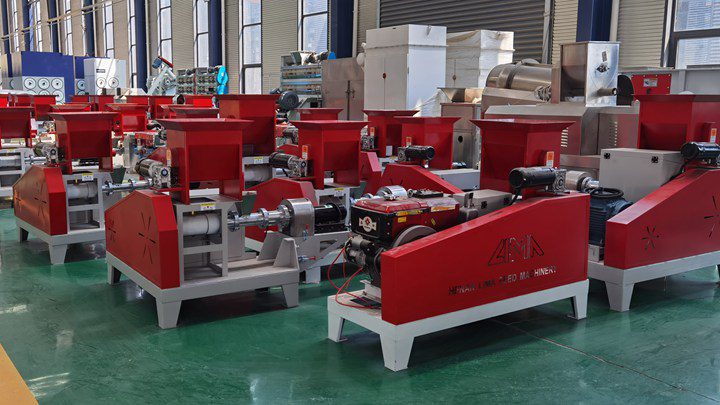
6. Adjust the gap between the ring die and the pressing roller every shift. If the machine is blocked, the pressure roller must be loosened, and the gap between the die rollers must be readjusted after removing the materials on the inner wall of the ring die.
7. Avoid overloaded production. During the production process, the working capacity of the granulator itself cannot be exceeded, otherwise, motor damage and accelerated wear of components will occur, shortening the service life of the granulator.
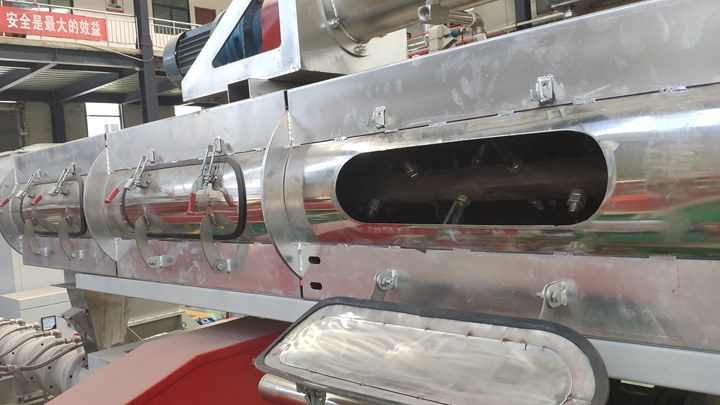
8. The raw materials must be cleaned of iron and impurities, and the iron removal device must be cleaned once per shift to avoid foreign matter entering the mold studio, causing the body to vibrate and the ring mold to crack.
Correct operation and attention to the maintenance of the floating fish feed extruder are the keys to prolonging the working life of the granulator. This requires strengthening the management of the equipment at ordinary times, and the benefits of the enterprise will be obvious.